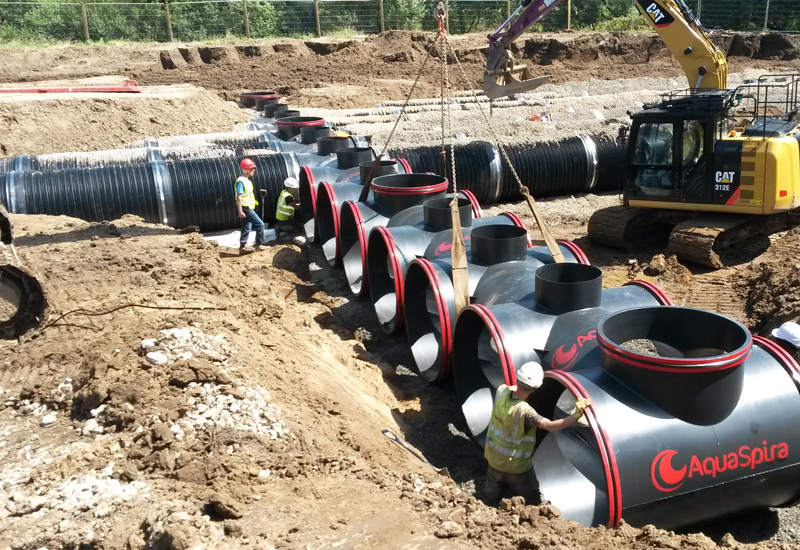
Mark Stanway, Director of AquaSpira explains how Composite Steel Reinforced (CSR) pipes were used at a development in Lancashire to manage stormwater run-off from the site.
The Links is a new Barratt Homes development in Garstang, Lancashire set on the banks of the River Wyre, overlooking the Forest of Bowland. The site will eventually accommodate over 130 houses ranging from 2 to 5 bedroom homes.
In common with all new housing developments, the ever-increasing requirement to manage stormwater run-off from the site needed to be addressed. The total volume of storage required was 1920m3 and for this particular development, due to the contours of the land and the position of the river alongside the site, into which the surface water ultimately discharges, the most appropriate solution for attenuating the surface water drainage was via the combination of a 1500mm diameter pipe connecting into a substantial below ground storage tank.
The initial design included a plastic pipe layout with a complex series of manifolds at both ends and at intermediate points within the layout. However, from a practical perspective, trying to knit together the variety of pipe runs and manifolds would have been difficult.
A further concern with the system originally specified was the requirement for on-site welding of the pipe joints. The tank was to be located in a low-lying area close to the river, and as such there was a high probability that the excavation would be waterlogged, making it almost impossible to undertake site welding.
Also, in common with many tank designs, sufficient consideration had not been made towards incorporating a good flow path for the drainage during predominant ‘low flow’ conditions, which is perhaps one of the most important aspects of design for the adopting Water Company.
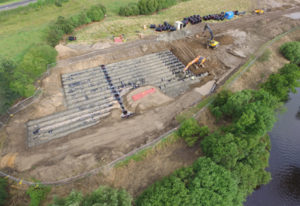
Storage solution
In view of the various concerns with the specified system, AquaSpira were invited to offer an alternative proposal, utilizing its Composite Steel Reinforced (CSR) pipes in conjunction with the company’s stainless steel manifold system. In total 1,100metres of 1500mm diameter CSR pipes was required to form the pipe leading up to the tank and to create an appropriate and acceptable storage solution.
In order to improve the hydraulic performance of the tank layout the design was adapted to create a single, primary flow path, from the inlet pipe at the upstream end of the tank all the way through to the downstream outlet, thereby minimizing the risk of silt build-up within the tank.
Central to the enhanced design of the tank, and efficiency of the installation of the tank, was the incorporation of a double-sided, 14 port manifold. To match the 120+ year design life of the CSR pipe, the manifolds were manufactured from a robust stainless steel material and then coated to provide a consistent appearance with the pipes.
The branches of the manifold were fitted with the same push-fit joints as the pipes including factory fitted seals and innovative bright red spigots to enable the installation team to clearly see that each joint had been made.

Delivery to site
The robust manifold was supplied in just two sections, each approximately 15m in length, but easily handled and lifted into position with standard site machinery. The manifold was set to line and level and, once in place, it was possible to commence installation of the pipes immediately.
Due to the robust construction of the manifold there was no requirement for any form of concrete surround, enabling the contractor to simply surround the manifold and adjoining pipes with ordinary pipe bedding material.
With the manifold and adjoining pipes in position, civil engineering contractor, Eurogold Groundworks & Civil Engineering, set in motion a planned and highly efficient procedure for scheduling, offloading, handling and installing the 415 pipes required to complete the works.
Each load, containing eight pipes, was safely offloaded in approximately five minutes by a small site machine with a simple pole attachment. Weighing in at just 237kgs, the pipes could be handled and moved to the position where they were required by small site machines, leaving the large machines free to maximize the speed and efficiency of the excavation works.
Push fit joints
Supplied with push-fit sealed joints the pipes were installed with the aid of AquaSpira’s Jointing Frame. On average, the single gang responsible for installing the pipes was able to excavate for, install, and backfill 20 pipes per day, irrespective of the weather conditions and despite the bottom of the excavation being routinely waterlogged.
Whilst Eurogold had recently converted to using AquaSpira large diameter pipes in place of concrete pipes this was the first of the company’s tanks that the company had installed. Site foreman Carl Nickson commented: “the manifolds were much sturdier than anything I have installed before. We had them in place within an hour or so and set about connecting the first pipes straight away. I hadn’t installed AquaSpira pipes before but colleagues from other sites had told me how much better they were to lay than concrete pipes.”
Carl continued: “based upon experience of installing other pipe systems we planned to install about 15 pipes per day, but once we got going we were able to install up to 24 pipes a day, mainly due to rapid connection of the push-fit joints.”
Having completed the installation ahead of programme, and with the area backfilled, Carl concluded: “Job done… and knowing how saturated the area can get during heavy rain, it’s a big relief to know that all the joints are sound and we don’t even have to think about having to organize and oversee in-situ joint welding, which in such wet conditions would be difficult to say the least.”
A brief video featuring the installation of the tank can be seen on AquaSpira’s website: www.aquaspira.com