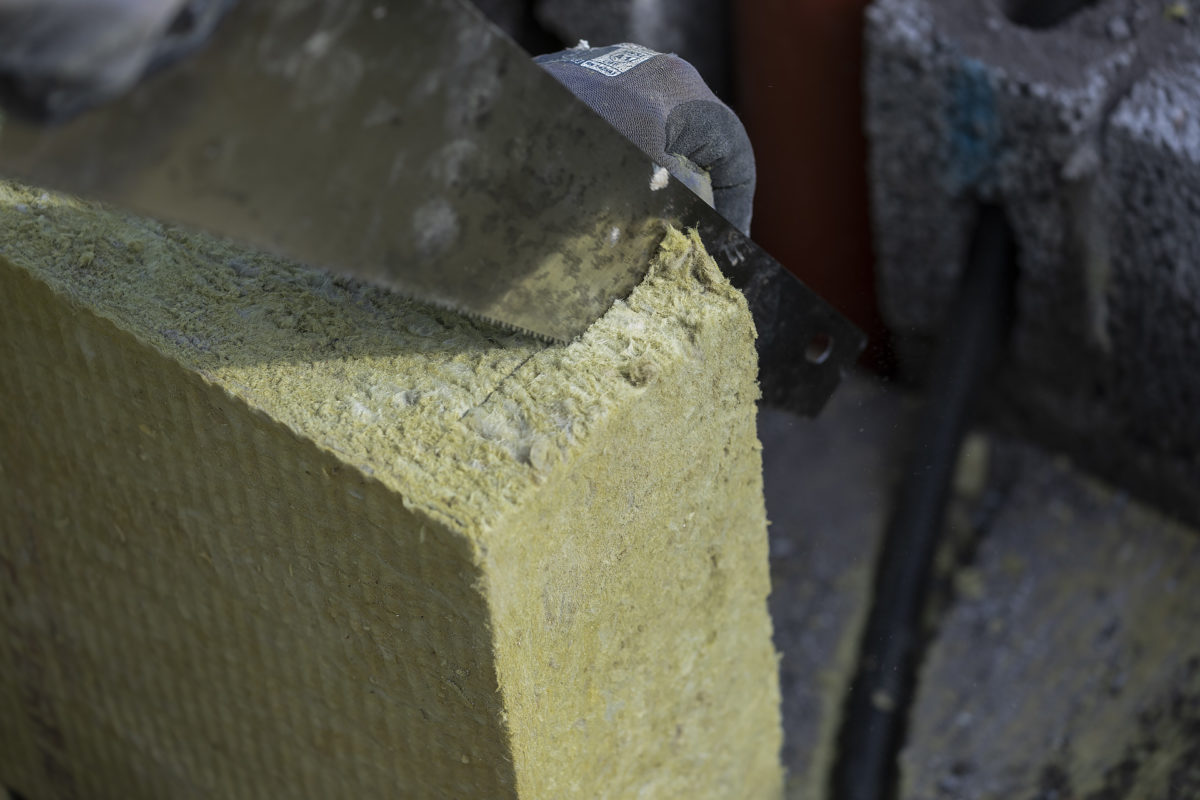
Paul Barrett, head of product management at Rockwool UK, explains why housebuilders need to think differently about insulation to meet legislative and buyer demand.
Historically, choosing insulation has, broadly, been a box-ticking exercise; select the product that meets the required U-value and move on with the development. However, thermal performance requirements are evolving, and so too are buyer demands for insulation with a desire for more than just thermal capabilities.
Legislative drivers
One of the drivers for this shift is Government legislation. This month (June 2023) sees the transitional arrangements for Approval Document L (ADL) end, meaning all building works in England that start after mid-June must now meet the latest regulations.
As part of ADL 2021, there is greater scrutiny of the gap between designed and as-built performance. Now, on completion of work, a Buildings Regulations England Part L (BREL) report and photographic evidence are needed. This evidence will be provided to the building control body to demonstrate compliance with energy efficiency requirements. Photographs must be taken at various construction stages before elements are concealed to show build quality and that the designed details have been followed.
This means developers, and for insulation specifically, will need to show evidence of the thermal continuity of the material at foundations/structures, external walls, roofs and openings, pipes and ducts to demonstrate it is fitted tightly and without gaps.
While already best practice for installation, the need to physically evidence continuity increases the need to achieve a tighter, continuous fit and could require additional cutting on-site and/or taping at board joints with foil tape. For housebuilders acutely aware of build schedules, this requirement could equate to extra time completing a plot and a more significant burden to ensure building control sign-off.
The ease of achieving this level of precise fit and, in turn, as-designed performance varies depending on the type of insulation used and selecting a product solely based on a single metric, such as its thermal conductivity, overlooks this critical consideration.
For example, pliable stone wool insulation is simple to closely friction fit without impractical levels of precision cutting when on site. As well as minimising the margin for error, it also supports reliable and effective thermal performance that reduces thermal bridging. Further, the flexibility of stone wool allows for easier installation at the abutments between insulation boards, another area prone to thermal leakage. Plus, its composition means individual slabs knit together to create a seamless fit, and its workable nature supports the delivery of designed U-values.
Performance in-use
The shift to consider longer-term, post-occupancy performance brought about by ADL is also a trend that’s likely to continue as legislation such as the Future Homes Standard comes into law. Reports such as that from the Committee on Climate Change also reference the role of smart meters and their ability to ‘track progress in, and performance of, energy efficiency and heating measures.’
Whether in the future, housebuilders may have greater accountability for a home’s energy performance once in use remains to be seen. Still, there is decidedly a shift in buyers’ considering a home’s energy performance and its impact on their future bills. Equally, several major housebuilders are marketing the ongoing energy bill savings that buying a new home can bring.
When selecting insulation, it pays to have longevity in mind as the thermal performance of some insulation types can wane over time. For insulation to be effective – and remain so – dimensional stability is vital as the air pockets within it help prevent heat transfer. Squashed and sagging insulation can affect these energy-saving capabilities.
To prevent this, it’s essential to choose a product that’s going to keep its strength and, in turn, its thermal performance. Stone wool is ideal for this as it maintains its shape and density over time. In tests on materials from real-life construction sites, it has been shown to retain its insulating properties for more than 65 years without a drop in performance. Plus, because of its high-density semi-rigid composition, it will not slump in the cavity.
Buyer demands
As well as greater awareness of energy performance – our research found that energy efficiency ratings are important to 76% of consumers when buying or moving home – consumers are also more discerning regarding new build quality. This greater scrutiny and a competitive housing market for attracting buyers mean that housebuilders need more differentiation than ever; an area where insulation can support them.
Following the Grenfell disaster and the subsequent ban on combustible materials in relevant buildings above 18 metres in England and Wales and 11 metres in Scotland, there is growing public recognition of building fire performance. As such, providing surety on fire resistance, even in low-rise housing, could help developers offer an additional marketable benefit. Manufactured from naturally occurring volcanic rock, stone wool has a natural, innate non-combustibility, with many stone wool solutions achieving a European Reaction to Fire Classification of A1 – the highest possible rating.
Similarly, stone wool provides acoustic performance due to a non-directional fibre orientation and increased density that traps sound waves and dampens vibrations, significantly reducing noise between rooms and from outside sources.
By considering insulation as much more than just a thermal insulant, housebuilders can achieve greater standout and improve the overall quality of their developments for buyers and years to come.
For more information, go to www.rdr.link/xxx