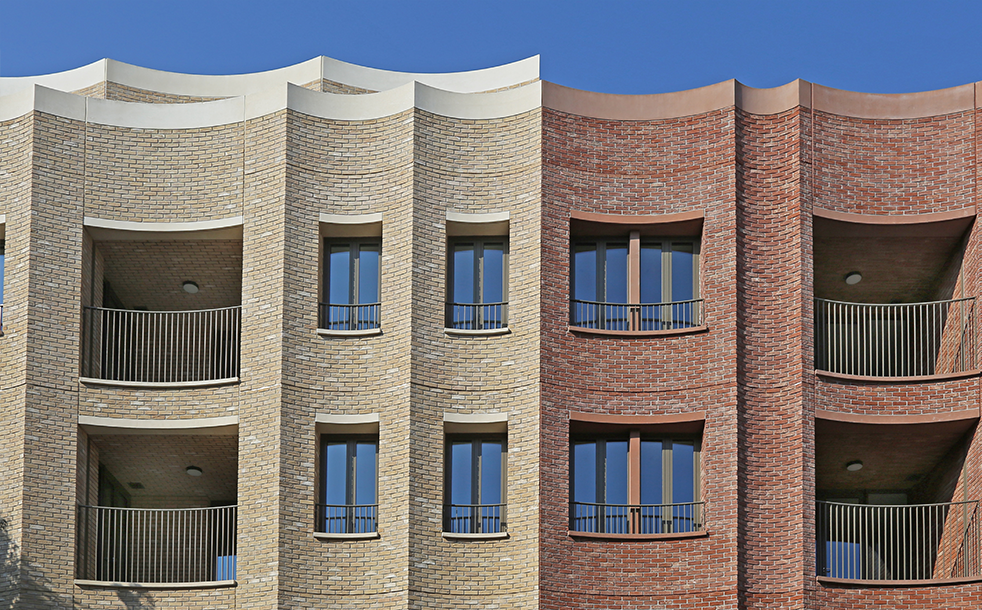
Creating new homes in London with off-site construction and Vandersanden.
One of the first residential developments created and offered for sale by Westminster City Council, Cosway Street, in Marylebone, London is a collection of 49 contemporary homes set around an attractive communal garden. Vandersanden’s Cayenne, Woodland Mixture and Lima bricks are integral both to the pre-cast Design for Manufacture & Assembly (DfMA) panels, forming the facades, and the traditional hand-laid brickwork lining the balcony spaces.
This landmark building was inspired by the area’s Georgian terraces and Victorian mansion blocks. From the choice of materials to the precise proportions and the gentle curves of the scalloped panels, every element of the architecture has been considered to help stitch the scheme into its setting. The design for Cosway Street was by Bell Phillips, realised by Osborne and their delivery architects David Miller Architects.
David Miller Architects took over the project post planning approval. The design intent was to craft the building as if it had been carved from brick. A key decision was to employ prefabricated DfMA brick panels for the main facades, alongside traditional hand-laid brickwork for the inset balconies. Using this approach allowed the construction team to build quickly to a precise, high quality and efficient standard in a controlled manufacturing environment, using less energy and carbon and creating less waste.
The idea was to split the building’s mass using the materiality, colours and textures of the three different bricks and the scalloped form of the panels to respond directly to the context of the site. The choice of bricks was incredibly important and had to meet the planning design intent explains Sundas Rohilla, project architect at David Miller Architects.
“It was essential to ensure we were picking up the right tones of reds, yellows and greys from the existing buildings; Vandersanden’s Cayenne, Woodland Mixture and Lima do this perfectly. They also harmonise with the pigmentation of the concrete sills and copings, as well as with the window and balcony railing colours.”
The mass of the building is reduced not only by the different blocks of brick colours but also by the gradation of the mortar colours across the façade. In all, there are five mortars with the darkest at the base of the wall and the lightest at the top. Using mortars in this way meant that there was no need to use different brick types to achieve the same effect, but it did mean that it was essential to have bricks of the right texture and consistency. The brick panels were pointed off-site in the factory.
The bricks used by Decomo in Belgium exactly matched those being used on-site by the bricklayers, with Vandersanden working closely with the design team and directly with Decomo to manage this process.
“Vandersanden was incredibly helpful and responsive from the start, providing samples and initial quotes during brick selection,” notes Rohilla. “The company’s approach to sustainability and collective wellbeing resonates with ours as an architectural practice. Knowing that Vandersanden has Environmental Product Declarations (EPDs) that are super open means that we can easily compare against other products. It feels like sustainability is really embodied into their culture.”
For more information on this project visit the Vandersanden website.