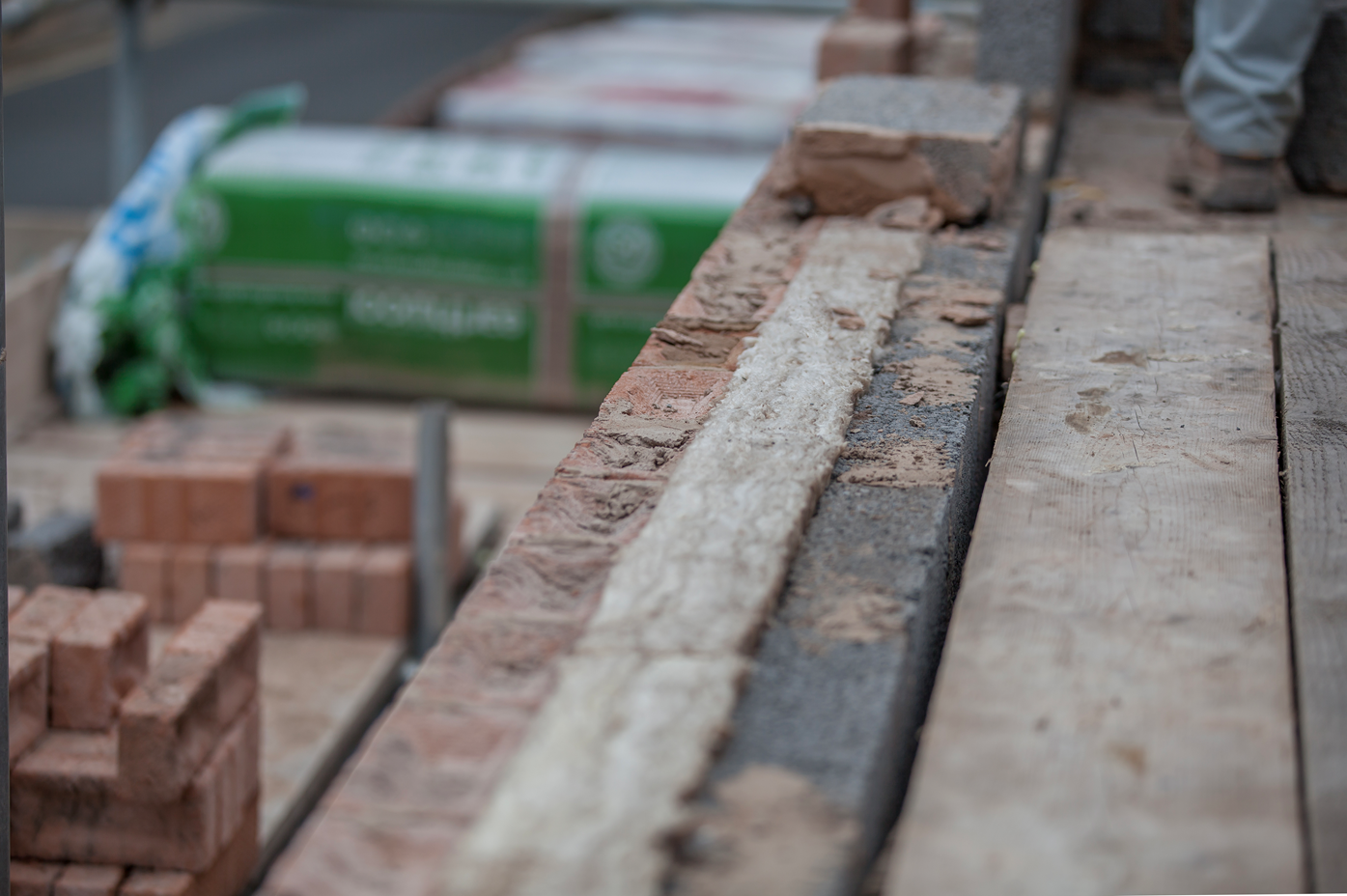
Matthew Prowse, specification and housing director for Knauf Insulation, discusses the changing Building Regulations and how housebuilders can keep ahead of the curve as the industry evolves.
This month marks a year since the introduction of uplifts to Part L (Conservation of fuel and power) of England’s Building Regulations and, consequently, the deadline for compliance. As of June 15th, all new homes must produce 31% less CO2 emissions and meet higher fabric efficiency standards, to name just two of the changes.[1]
There’s been a lot for the industry to adapt to, but this is still only a transitional step towards a more ambitious goal. By 2025 the CO2 reduction figure for new homes will shift to 75%[2] and the only way to achieve this is with a ‘fabric first’ approach.
As regulatory changes gain momentum over the coming years, how can you ensure your specifications keep up?
Cavity width
Some housebuilders have been understandably reluctant to increase their cavity widths up to this point. But whilst it’s possible to achieve Part L compliance with a 100mm cavity, it limits your options and could result in costly redesigns as regulations evolve.
A thickness of 150mm will provide optimal fabric performance and when the Future Homes Standard arrives in 2025, most homes are likely to be built with a wider cavity. Adding an extra 50mm now has a minimal impact on floor space and gives you more insulation options to choose from.
A home’s energy efficiency relies as much on correct installation as it does on the insulation itself. Lambda values are important, but they only tell you the potential thermal performance of a product. Whether this is met in the real world depends on how it’s installed. Rigid foam board insulation is a good example; unless a cavity is perfectly uniform and flat, rigid boards won’t sit flush against it. Joints between boards also need to be taped with precision, leaving ample room for human error. This can lead to unintentional air gaps, which reduce thermal performance. Mineral wool on the other hand is flexible and will adapt to minor imperfections in the substrate, minimising gaps and maximising performance. Its ‘buildable’ nature makes mineral wool easier to ‘get right’.
The bigger picture
Energy efficiency isn’t the only item on the agenda for change. Part B (Fire safety) for example, now requires all residential buildings between 11m and 18m to use non-combustible materials in certain external wall system build-ups, such as rainscreen façades and timber frames, unless a full-scale fire test to BS 8414-1 or BS 8414-2 has been conducted[3]
With so many moving parts to consider, it makes sense to choose products that tick multiple boxes and are likely to stand the test of time. Mineral wool by its nature is non-combustible, easier to install correctly, and it can be used in both larger and smaller cavities, in any building of any height. That’s why it’s the reliable choice for Part L and beyond.
[1] Approved Document L.
[2] Future Homes Standard.
[3] Approved Document B.
For more information on Knauf Insulation, go to www.rdr.link/xxx