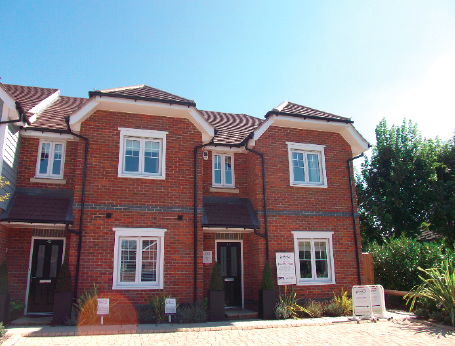
Time is ticking on the journey to net zero, but for housebuilders and developers, it’s not a journey they need to make alone, says Colin St John, Commercial Director of Freefoam Building Products, which manufactures and supplies fascias, soffits, and rainwater to housebuilders in the UK and Ireland.
Read any consumer survey about what buyers are looking for in their next home, and you can be sure that energy efficiency and sustainability are among the top considerations. For housebuilders, developing properties for eco (and bill) conscious homeowners is now a realistic option as many manufacturers and suppliers have upped their game to offer products which save energy or improve a building’s performance, spurred on by the government’s 2025 Future Homes Standard, which focuses on improving heating, hot water systems, and reducing heat waste.
However, emissions generated from the use of a home are only one aspect of its sustainability credentials. The materials and energy used to create each building product and transport it to site can be just as important. An industry-proposed amendment to the Building Regulations, Part Z, just a concept now, has proposed mandatory assessments and reporting of ‘whole life cycle’ carbon, reducing ‘embodied’ emissions from materials and construction.
Emissions generated by suppliers are referred to as Scope 3 greenhouse gas emissions. For housebuilders to build and market homes as truly sustainable, decarbonisation of downstream emissions is essential. This isn’t mandatory, but as Scope 3 emissions account for between 80-95% of a total value chain of an organisation’s footprint, it’s likely to be legislated for in future, just as Scope 1 (direct emissions) and Scope 2 (indirect emissions) reporting is for bigger organisations now.
Suppliers should do the heavy lifting in reviewing and reducing Scope 3 emissions. They confirm their environmental impact, and housebuilders can then decide to stick with them for the overall sustainability of their business and their homes or switch to a ‘greener’ product/supplier.
In roofline and rainwater, there are some key green credentials housebuilders and architects can look for in a supplier:
ISO 14001
This accreditation is the internationally recognised standard for environmental management systems (EMS). It’s used as a benchmark for many businesses to show how they are reducing their emissions and environmental impact.
EcoVadis rating
The world’s largest sustainability ratings provider, EcoVadis has assessed more than 100,000 companies. Ratings are based on the actions taken to support objectives around the environment, labour, business ethics and sustainable procurement. Housebuilders should ideally be sourcing from Gold and Silver accredited suppliers.
Climate Change Agreements
Climate Change Agreements (CCA) are voluntary agreements between UK industry and the Environment Agency to reduce energy use and carbon dioxide emissions. Any supplier with a CCA must measure and report energy use and carbon emissions against agreed targets.
Supply Chain Sustainability School membership
The Supply Chain Sustainability School is a learning platform dedicated to upskilling people within the built environment. It covers the three pillars of sustainability – environmental, social, and economic, with companies awarded attainment levels.
Suppliers who actively engage with the SCSS demonstrate a clear commitment to supporting team members and embedding sustainability into everyday work practices. Reducing emissions across the building supply chain is everyone’s responsibility.
Only when we work together can we make 100% sustainable homes, down to the last nut and bolt.
More information on Freefoam Building Products