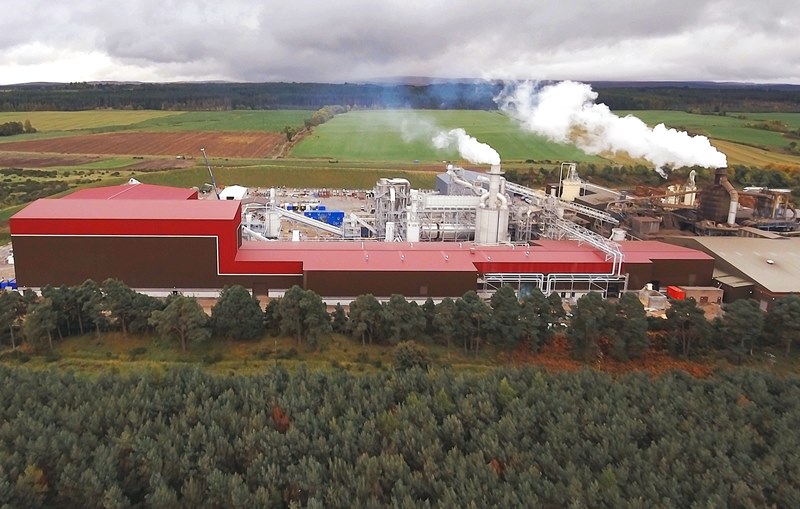
PHPD recently visited the Norbord timber mill in Inverness to discover how a £95m investment in the latest production technology is set to almost double its output of OSB.
Material shortages and prices rises are always a concern for the construction sector. In a recent FMB State of the Trade survey, 90% of builders reported increasing material prices in Q1 2018. Left unresolved these factors could inhibit housebuilding growth. It was a pleasure, therefore, to visit Norbord’s Inverness timber mill, where a £95m investment will see the company dramatically increase its output of Oriented Strand Board (OSB).
An increasingly common material found not only in roofing and flooring, OSB is increasingly being used in, amongst other areas, kitchen cabinets, site hoarding and furniture. Norbord is one of the world’s largest manufacturers of OSB, with European production taking place in plants in Genk, Belgium and Inverness.
In 2015, the company announced a £95m investment in the Inverness facility to dramatically increase its OSB production capability. The decision reflected continuing growth in the OSB market which saw a double digit percentage rise in OSB demand across Europe between 2012 and 2015 – a demand that has continued ever since.
Commenting on the investment announcement in January 2016, Karl Morris, Managing Director of Norbord Europe, said: “Demand for OSB is increasing rapidly and this investment will ensure we can continue to meet customers’ needs and remain at the forefront of the European industry.”
Official opening
The new plant began production testing in September 2017 only 8-10 months after the first steel structures were in place. It was officially opened in April 2018 by Scottish First Minister, Nicola Sturgeon MSP. She said: “Norbord’s £95m expansion of its Dalcross plant is one of the largest single inward investments made into Scotland. It will significantly increase capacity and demonstrates the vibrancy of the Scottish forestry sector.
“This is a welcome investment for the Highlands that will secure a long term future for the factory. It has received more than £12m support from Highlands and Islands Enterprise and is expected to generate £37m gross value added of new economic activity for the Scottish economy each year.”
Karl Morris added: “The launch event was the culmination of several years of work to dramatically increase the capacity of the plant and a fantastic celebration of our investment and commitment to Inverness. It was a pleasure to welcome the First Minister to witness first-hand the positive impact the project is having on the community. The new line will help ensure we continue to be a leader in OSB production by meeting our customers’ increasing demand for the product.”
Production capacity
Initially the new plant operated in parallel with the mill’s existing production lines, but in mid-May the old capacity was turned off, with output from the new single continuous press plant overtaking that from the two older lines. But that is only the start – it is anticipated that the new plant will soon be capable of producing 640,000m3 of OSB, almost double the Inverness plant’s capacity in 2015.
Although OSB is now a familiar building material used on thousands of jobs every year, it only became a mainstream product in the UK a little over 30 years ago. In fact, the Inverness mill was the first factory in Europe that made OSB, beginning production in June 1985. In its first full year of production around 60,000m3 of OSB was produced. Following the recent investment, production is anticipated to be 10 times that original capacity.
Sterling OSB zero
Norbord’s OSB product is widely known as SterlingOSB, or sometimes Sterling board. With the introduction of the new plant, the company is renaming the product it produces from the Inverness plant to SterlingOSB Zero. The ‘zero’ reflects the fact that by using the latest technical innovations, the new facility can make OSB without the including any additional formaldehyde in the resin used during the production process.
This development reflects a growing move towards the use of less environmentally harmful materials in the construction process. Although formaldehyde is naturally present in the human body, increased exposure to high levels of formaldehyde can result in asthma attacks, nausea, headaches and respiratory irritation.
Simon Woods, Sales, Marketing and Logistics Director for Norbord Europe, explained the significance of this move: “SterlingOSB Zero allows Norbord Europe to offer OSB product to all markets that we operate in. The benefit of zero-added formaldehyde product significantly reduces the emissions of formaldehyde across all parts of the production and usage process – production of the finished material, manufacturing of products from the OSB boards and at the end-user or consumer.”
Further investment
With the company now producing OSB from its new continuous press, the old machinery is being decommissioned and removed. Norbord has plans to use this space to replace its finishing lines – where tongue-and-grooved edges and special finishes are applied to the board.
The new finishing lines, together with the continuous press, may also open up further market opportunities for Norbord’s OSB in the future.
Norbord’s £95m investment in its Inverness plant will ensure it continues to deliver high-quality OSB products for the construction sector. It also demonstrates the company’s commitment to the UK timber market for years to come.
For more information visit www.norbord.co.uk