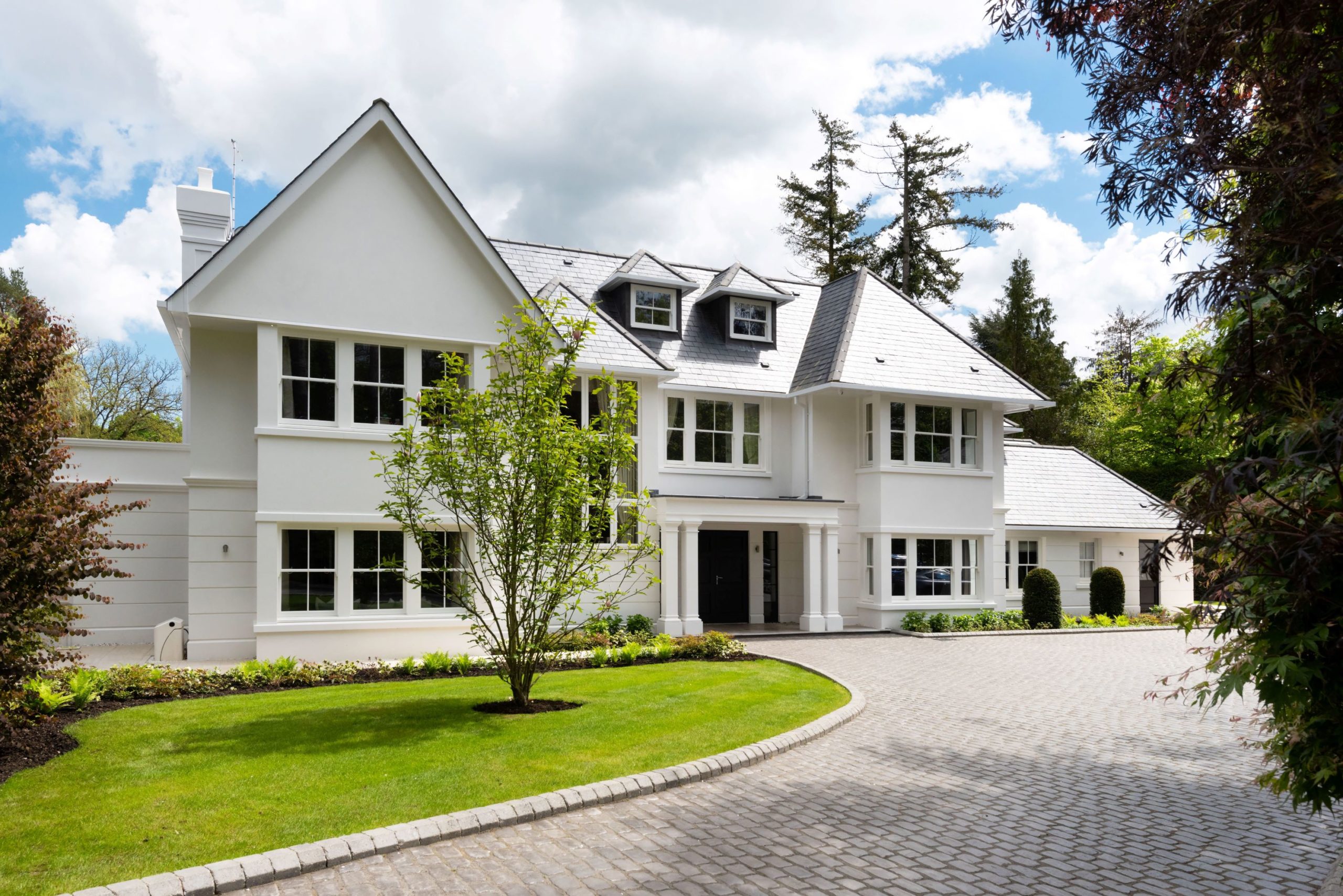
David Barrow, managing director of Haddonstone, casts some light on the subtleties of reconstituted stone, and the potential applications for the products. Traditional stonework may be viewed by many as the optimum choice of exterior finish for many period and contemporary style properties, but the quarried material inevitably features many inconsistencies, while the additional hours required for skilled masons to complete its installation make the overall cost prohibitive for most developments.
It is, therefore, the consistency, comparative strength and all-round buildability of the factory-manufactured alternative which keeps the members of the UK Cast Stone Association in business, and very much in demand.
To get the best from the various types available, however, it is important to understand how they are produced: and therefore, why they will be suited to different applications across the built environment. Furthermore, it is a technology which continues to be refined in response to both practical and environmental challenges.
Starting with the raw materials which are employed by all the manufacturers in varying proportions, limestone is a type of sedimentary rock which occurs worldwide, though the UK’s geological history provides us with some unique deposits such as Cotswold Limestone with its distinctively coarse ‘oolites.’ Cast stone companies prefer the smaller finer grained varieties like Bath Stone, crushed to different grades.
These are mixed with silica sand which aids compaction and densification, while sufficient Portland Cement is required for the mixes to attain the minimum strengths set out by the UKCSA’s guidelines. The mix is normally hydrated with water and with additives also being incorporated to improve plasticity without diminishing the compressive strength.
Although some producers utilise basic sand/cement mixes, the product ranges incorporate 60% of well-graded crushed limestone, with the particle size reducing from 3mm down to flour-like grains for the best outcomes. The mix is dry packed into moulds, normally with mechanical rammers, and left to cure overnight before being turned out. The units then spend a second night in in vapour curing chambers to speed the process.
With good quality control, the 35N minimum strength required for semi-dry cast should be easily exceeded, while water-proofing admixtures help protect against frost to ensure the appearance and weathering characteristics are close to those of cut stone. As a result, semi-dry cast is favoured for a very wide range of applications from garden ornaments through to window dressings such as cills, quoins, heads and surrounds, wall dressings including copings, pier caps and finials, entablatures, columns and grand porticos.
Wet cast products have a mix design that incorporates a slightly higher percentage of limestone, which in turn features a particle size peaking at some 10mm diameter. The biggest contrast to semi-dry cast is the use of super-plasticisers which give the mix a consistency, or slump, close to that of the structural concrete normally delivered to site. This consistency means the material is self-compacting when poured into timber, fibreglass or rubber moulds and can therefore produce more complex and even undercut or concave profiles. The moulds, meanwhile, are filled on tables which gently rock to release air which could otherwise create an inconsistent surface.
Wet cast products are released from the moulds after a similar 12-hour period but do not require vapour curing and are expected to achieve a compressive strength of 45N. They are, though, finished in sharply contrasting ways, with some manufacturers preferring to lightly sandblast the surface, while others apply a dilute hydrochloric acid. This is then rinsed off before the process water is treated to protect the environment.
The higher strength and production methods offer wet cast some significant performance benefits compared to semi-dry cast: including improved durability while the ability to insert steel reinforcement greatly enhances spanning capabilities as well as overall load carrying strength.
Offering greater strength than cut stone, wet cast can be used for decorative lintels and beams spanning significant openings in façades, as well as for eaves details, cornices, fountains, finely detailed statues and ultra hard-wearing floors or steps.
The final category of architectural reconstituted stone encompasses fibre-reinforced cast stone, such as TecLite, combining sand, cement, water and plasticisers to achieve a mix which can be poured into moulds, creating shell thickness from 20mm.
While the costs are comparable to wet cast products, their lightness often sees fibre-reinforced products chosen to overclad and enrich the façades of buildings where limitations on total weight or handling restrictions exist. Produced using moulds, they are also popular because of the contemporary designs which can be produced.
It should be realised then that whether you are involved in refurbishing a heritage building or building an estate of Edwardian or Georgian style homes with Greco-Roman statuary around the landscaped gardens, reconstituted stone in its various forms present a versatile and affordable design solution.
Want to know more?
For more information on reconstituted stone products, click here