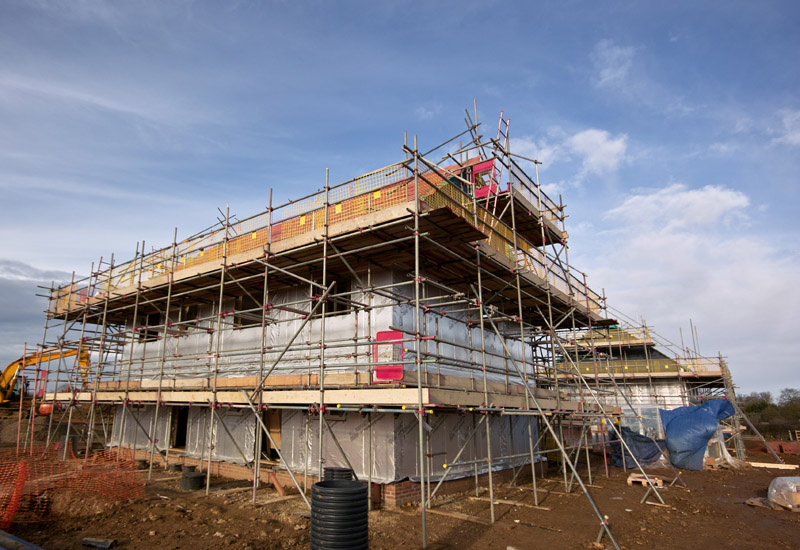
Alex Goodfellow, Group Managing Director of Stewart Milne Timber Systems, highlights why offsite construction and timber systems are the best choice for housebuilders increasing volumes.
For housebuilders in growth mode, the main aims are usually to build efficiently, manage cash and generate profit. Key areas of the business will focus on challenges: how quickly can the main structures be erected to meet build programmes and sales demand? How many skilled trades are required and for how long? Will the project remain cost-effective and on budget? How can quality be guaranteed? Is there enough capacity to ensure growth is not restricted?
The answer to all of these questions is to use precision-engineered timber systems and offsite construction.
The demand for new homes hasn’t reduced and with Government ambitions to build 400,000 new affordable homes by 2020, housebuilders are seeking out ways to achieve that volume in a cost-effective, profitable way all while protecting the quality of the build.
Timber systems allow housebuilders to build with a tried and tested, fabric-first solution to overcome the pressures they face in terms of capacity, speed, cost, and quality. It is the simplest, quickest and most cost-effective solution for housebuilding and utilises a low-carbon, sustainable and readily available material to help produce high-quality homes at a high-volume.
Speed up
At our factories in Witney and Aberdeen, Stewart Milne Timber Systems can guarantee manufacturing capacity for housebuilders. We have the ability to produce 10,000 timber units per year and can flex our manpower upwards to accommodate larger projects and shorter lead times. With our integrated supply chain, we can meet housebuilders’ exact requirements across the UK and beyond with ease. In just one day, our factories can produce 28 timber kits with the ability to double capacity if required. We also have long-term availability for materials and, if needed, we can guarantee call offs with three weeks’ notice.
Using timber systems and offsite construction, the speed at which the main structures can be erected significantly increases. Manufacturing offsite means ten blocks of terraced houses can be erected five weeks earlier than if building with masonry or other on-site solutions. In addition, once on site, a typical four bedroom detached home can be erected, wind-protected and made watertight in as little as five days.
Skills shortage
Beginning new developments in the midst of a skills shortage can be a concern for housebuilders, and there are inevitably cost pressures during large-scale building projects. But using offsite construction can reduce both labour and material costs as there is less reliance on trade skills and on-site supervision. The faster build of the main timber structures reduces the management required to supervise and co-ordinate on-site trades. The accelerated build time provides a quicker return on capital outlay, and site prelim expenditure can be reduced by up to 30%.
Using timber systems and offsite construction, a home can be designed as one integrated system. This means energy efficiency is locked into its core, reducing the need for other micro renewables or for new and un-tried ‘bolt-on’ technologies to be added to enforce energy efficiency. It’s a game-changer for the housebuilding sector as it requires homes to be built to capacity, especially during a time when there are skills and material shortages.
Value engineering
When housebuilders engage with us to produce timber systems for theirprojects, we get involved at the earliest point possible. This enables us to value engineer throughout the project, work with client teams to improve build programmes, deliver efficiencies and reduce cost. From initial concept and design stages through to construction on site, our project teams are highly experienced in their field, bringing their expertise to better meet the client’s exact requirements.
For housebuilders, there has never been a better time to consider offsite construction. It can contribute to a more efficient, sustainable, high-quality and cost-effective development. We invest significantly in research and development and we partner with various universities and housebuilders to develop new products to bring to market that, in turn, will add value to projects now and in the future.
One of our most successful product innovations is our award winning Sigma II Build System, a closed panel system that is BBA Certified and delivers performance standards to BREAAM Excellent status. Used for both housing and commercial projects, it has become a sought after product that also offers BOPAS accreditation.
No matter what the concern, whether it is cost, speed of build, quality or capacity, using timber systems can offer peace of mind from the very beginning of the project – delivering homes on time and on budget, every time.