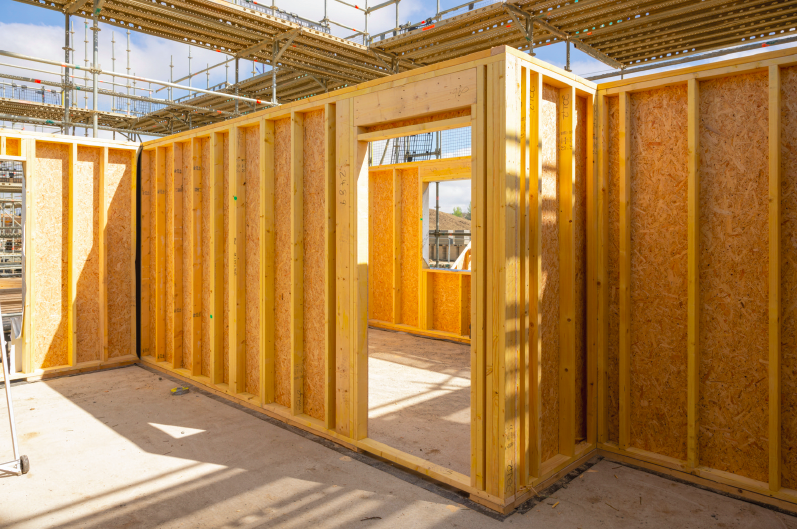
The journey to Net Zero is underway, but using current standards, new buildings may never achieve true zero carbon. Donaldson Timber Systems Technical Director, John Smith, explains.
While it sounds complex, the message is simple: without measuring and reducing the cradle to grave impact of a build, there is a very real risk that buildings constructed to new standards in 2026 and beyond won’t achieve true zero carbon.
On the face of things, it seems that the journey to Net Zero Carbon homes is progressing, with the first Building Regulation changes already in effect as we work towards the Future Homes Standard (FHS). From 2025, newly built homes need to be ‘zero carbon ready’, with a 75% reduction in carbon emissions to 2021 levels in England and Wales.
While this is a much-needed step in the right direction, more clarity is required on what it means to be carbon neutral. The new standards focus on reducing operational carbon, failing to recognise the impact of embodied carbon.
The reality of embodied carbon
Embodied carbon is the total greenhouse gas emissions generated during the construction and demolition phase. It is calculated in two separate elements: from raw material extraction through to construction of the building on site, including fuel and power for transport, factories and plant; and end-of-life emissions from demolition, transport from site and recycling / landfill.
In a new home completed to 2021 standards, embodied carbon is around 15- 20% of the whole life emissions, with the rest from operation carbon (energy required for heating, lighting and hot water). With a target to reduce emissions by 75% through operational carbon reductions, the embodied carbon becomes much more significant. By 2025, it will be over 40% of whole life carbon for a new-build, and over 60% by 2030.
Despite this, embodied carbon emissions are currently unregulated in the UK construction industry, with only voluntary measurement and mitigation required. The UK is lagging behind in this area. The Netherlands and Sweden already have mandatory embodied carbon requirements for all new buildings, with Denmark and Finland following suit. In France, embodied carbon in housebuilding has been regulated since 2022. This regulation addresses the entire life cycle of buildings and requires developers to measure both operational and embodied carbon. To comply, developers must perform Life Cycle Assessments (LCA), which evaluate environmental impacts from raw material extraction through to demolition or reuse.
Measure and reduce
As demonstrated elsewhere in Europe, the only way to achieve zero carbon is to measure and reduce the whole-life carbon of buildings. The availability of environmental product declarations (EPDs) is an important step in recognising this.
An EPD communicates the environmental performance of a product over its lifetime, making it possible to compare the impacts of different materials and products accurately and allowing customers to select the most sustainable option.
We’re investing in this process for all our products and were proud to become the first timber frame manufacturer to offer a published EPD for an off-site assembled timber frame wall panel. We always champion the use of offsite timber frame as the best way to achieve sustainable building practices, but a verified EPD proves these claims.
Time for timber
When we factor embodied carbon into the zero-carbon journey, timber comes into its own. Life cycle studies of timber frame homes show that they significantly outperform alternatives – saving around 40% of emissions in comparison to concrete and 30% compared to steel. Timber frame homes are more sustainable during the build, when in use and throughout its lifetime. Timber can also lower or offset its embodied carbon thanks to sequestration, absorbing one tonne of CO2 in every mÑ while the tree is growing and storing it until the timber is incinerated or goes to landfill.
Timber frame offers a safe, reliable, technical solution – homes have been built this way across the UK for years and we know that it works. At DTS, we have been working with our partners in the UK housebuilding market for almost 50 years. Our Sigma® II closed panel solution achieves FHS from the factory, with no additional works required on site, as well as very low levels of embodied carbon. Sigma® II has achieved a range of third-party approvals, including BOPAS Plus, BBA, NHBC Accepts and STA Gold Assure, delivering the confidence that it is durable and complies with building regulations and technical standards.
In missing embodied carbon, FHS has a major flaw. It aims for homes to be ‘zerocarbon ready with no further work needed’, yet by using these incomplete measurements, the carbon in the fabric will not be offset by even the greenest energy without improvements to the insulation and air-tightness.
With the Government committing to building 1.5 million homes in the coming years, embodied carbon must be legislated, or we’ll never achieve true zero carbon homes.
More information on Donaldson Timber Systems