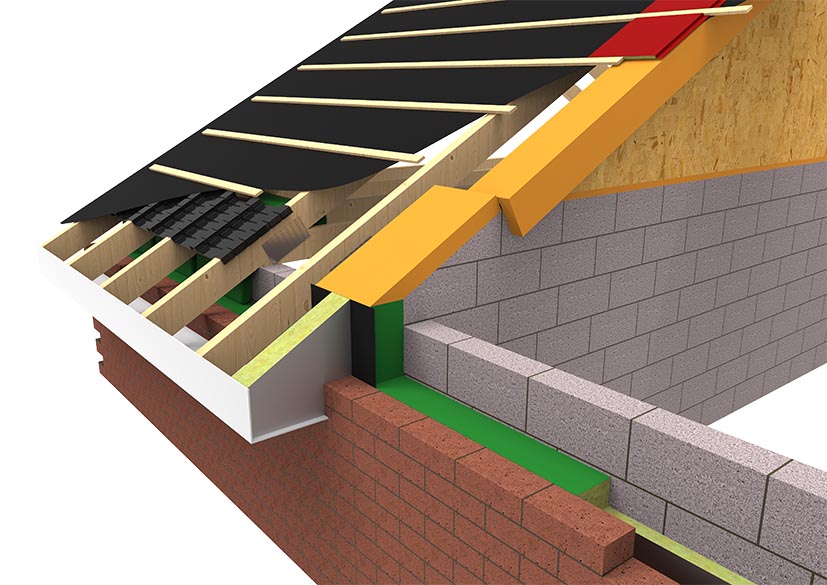
George Danzey-Smith TIFireE, Business and Technical Manager at ARC Building Solutions, discusses the benefits of taking a systems approach to firestopping and edge sealing at the party wall and eaves area to enable the build of high quality and safer new homes.
Internal and external wall cavities provide a means for fire to travel unnoticed throughout a building, spreading rapidly and bypassing compartmentation. According to Part L of the Building Regulations (England and Wales), measures must be in place to restrict the spread of smoke, flames and heat within the wall cavity and to improve the thermal performance when building a semi-detached or terraced property.
While there are no strict checks surrounding the use of cavity fire barriers, it is vital that housebuilders fully understand their importance and carefully consider the range of fire inhibiting products available on the market in order to improve the standards of safety and quality of new homes being built, as well as provide peace of mind to future homeowners.
In the party wall and eaves area, there are a number of risk areas that housebuilders need to factor into their designs in order to achieve an effective and compliant firestopping strategy. For example, the party wall cavity must be fire stopped around its entire perimeter and be incorporated at any separating floor or wall junction. In timber frame construction, it is also necessary to provide fire stopping around all window and door openings. As construction is evolving, we are seeing more developers opt to detail a spandrel panel as part of their party wall construction therefore it is important that appropriate fire stopping is installed between the spandrel panel and surrounding construction elements.
As cavity fire barriers have different functions according to where they are installed in the structure, it can be daunting for housebuilders to know which products to choose. However, housebuilders need not worry as specialist suppliers can now provide a ‘one-stop-shop’ single-branded system, which will allow an easy and systematic approach. All products within a system are designed and tested to work together, removing the need to meticulously verify that each element is compatible with the other. Such innovative systems bring together a number of products from a manufacturers’ portfolio, saving cost and time as all products are sourced from one supplier.
Whether you are working on a masonry or timber frame construction, there are systems that have been designed, engineered and rigorously tested to work together for both build types. By taking a systems approach, housebuilders can ensure that all elements are covered and provide complete protection by preventing the spread of smoke and flames to neighbouring properties.
Most cavity barriers also provide thermal insulation, therefore making properties more comfortable to live in, as well as reducing heating costs by controlling thermal loss. Noise pollution is also improved, with the barriers reducing sound transmission between terraced and semi-detached homes, for example. All products within a system are manufactured and engineered within set tolerances which makes it easier for the housebuilder, as they can follow one standardised set of guidelines when building new homes.
Housebuilders should seek advice from suppliers at the very beginning of a project, with early engagement key to achieving the most appropriate, best value solution. Look out for systems that have been independently tested and certified by a third-party certification body, such as Certifire by Warrington Fire, to assure the performance, quality reliability and traceability of the fire inhibiting products. What’s more, companies that can offer extensive technical support, training and resources will always be of benefit to developers and enable all parties to work together more efficiently.
Whilst specification of the right products is essential, ensuring that the products are installed correctly is just as important. Housebuilders should consider suppliers that offer support to installers through the publication of datasheets, videos as well as on-site training to advise and guide on products and the installation process.
One such development that is proving popular within the industry is the ARC Firestopping System for Party Wall & Eaves Area. Comprising eight key products in masonry construction and six key products for a timber frame construction, each product is installed as the build progresses and eases the installation process by providing a logical sequence. Developed in conjunction with leading academia from Leeds Beckett University, the system has been trialed successfully with leading housebuilders, who have found it to have contributed to an improvement in the quality of their builds.
Cavity fire barriers at the party wall and eaves area play a crucial role in the construction of new build homes and skipping this step can lead to severe consequences. As the topic of fire safety and quality continues to mount in the housebuilding industry, taking a systems approach to firestopping and effective edge sealing at the party wall and eaves area can protect people and property.