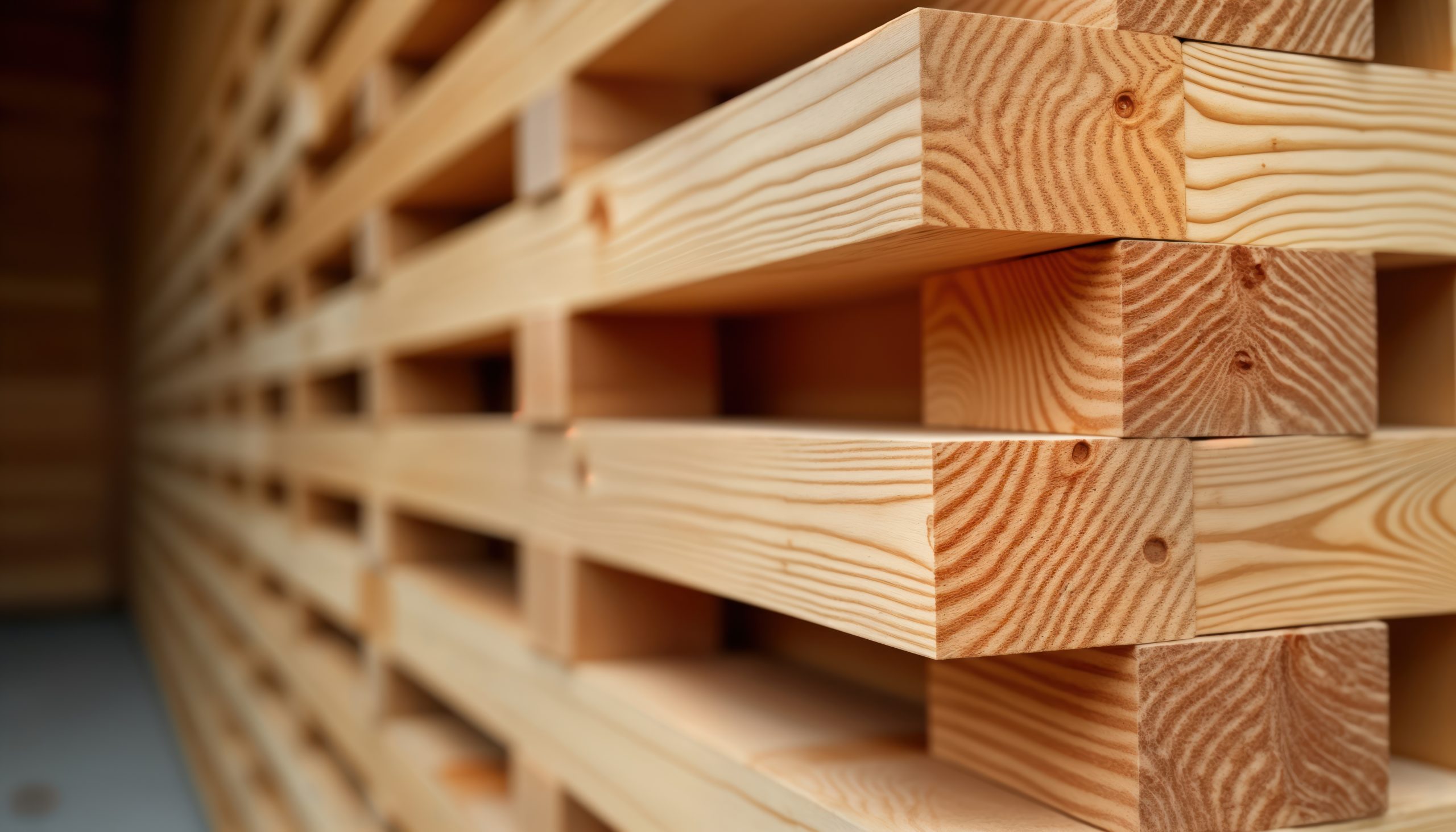
Alex Goodfellow, CEO of Donaldson Offsite and STA board member, discusses the commercial viability of structural timber in housebuilding.
The launch of the Timber in Construction Roadmap in late 2023, coupled with the Structural Timber Association’s (STA) implementation guides, signals a pivotal moment for timber in construction. These efforts aim to increase the use of timber in UK construction projects, aligning with the nation’s net-zero targets for 2050 and supporting government housebuilding goals.
Timber’s advantages go far beyond its environmental benefits, with time efficiency of timber construction being a key benefit. Timber-framed homes can be built in as little as 15 weeks, compared to the 26-30 weeks typical for masonry or concrete methods. This time-saving translates into significant cost benefits, reduced project risks, and greater certainty for housebuilders – a crucial factor in an industry that values efficiency and predictability. Not to mention the time taken to make the house weather-tight is between 6 to 10 weeks shorter than with masonry, allowing internal works on the critical path to start and complete much earlier.
Additional benefits of timber systems include reduced waste, minimal landfill contributions, and fewer weather-dependent delays. Offsite manufacturing’s “just-in-time” approach enhances project management, enabling shorter build times and lower costs. These operational efficiencies make timber a commercially attractive option, especially in affordable housing and high-volume projects.
While the UK imports 80% of its timber, primarily from Baltic countries, the supply chain remains robust. Swedish sawmills and other suppliers are prepared to meet increasing demand, despite the need for imported materials. The STA is optimistic about the industry’s readiness, noting an increase in timber house frameworks and capacity for greater output. Domestically, efforts to expand the UK’s forestry output are underway, but the long cycle of forest maturity means imports will remain essential. Nonetheless, timber construction’s carbon footprint is significantly lower than concrete or steel, even when accounting for transportation emissions.
With strong supply chains, eager manufacturers, and increasing market acceptance, timber is poised for growth. The STA’s guidance ensures businesses can navigate this transition with confidence, highlighting timber’s commercial viability and its potential to transform UK construction.
More information on Structural Timber