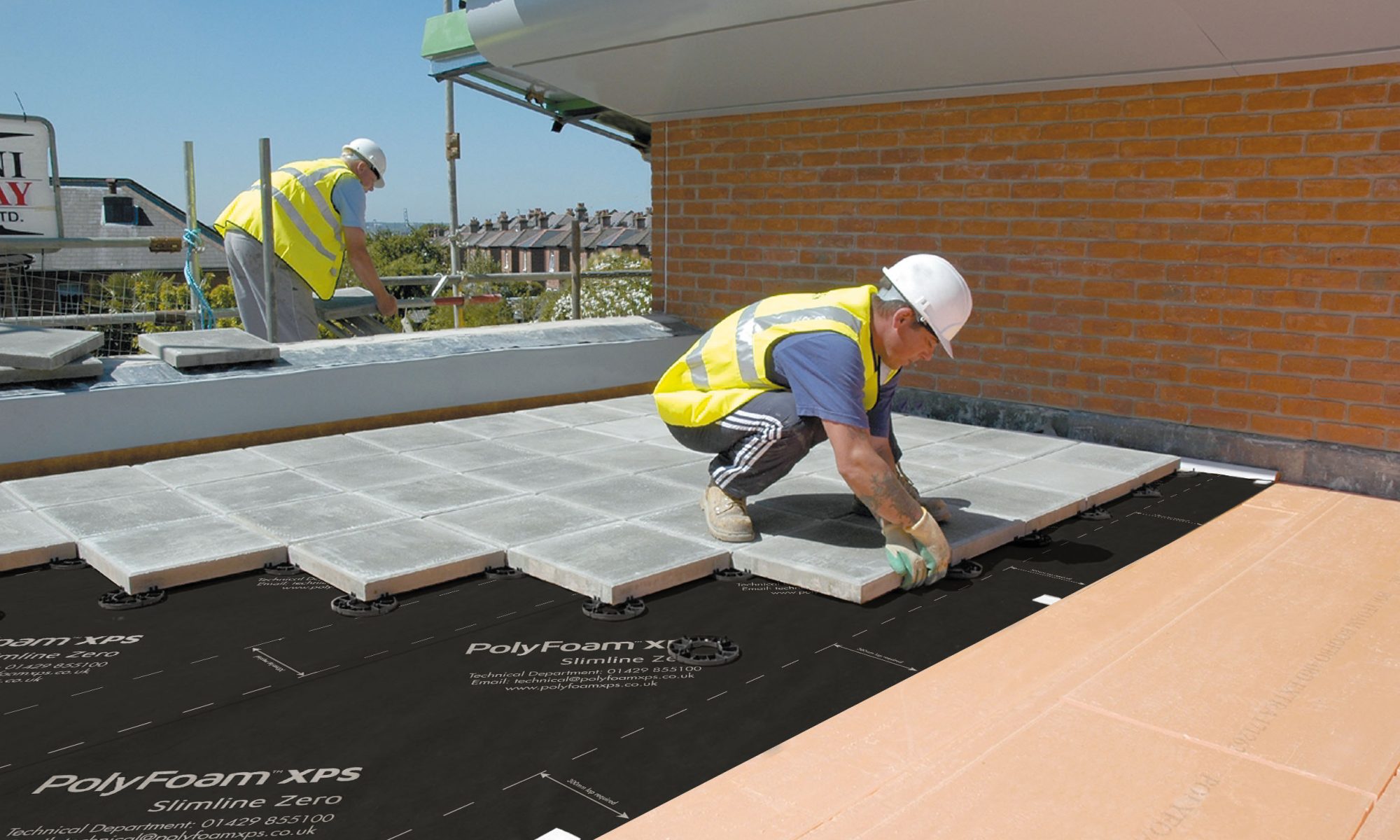
The main function of thermal insulation is to provide thermal performance, so products are often specified for efficiency first and compressive strength second.
This can result in the specification of insulation with good thermal performance but distinctly average compression behaviour, says Rob Firman, technical and specification manager at Polyfoam XPS.
Insulation products must be capable of bearing the loads imposed on them. A better understanding of compressive strength declarations can help with making more informed decisions at the design and specification stage. It can also avoid changes being made on site that could result in a shortfall of both thermal or compressive strength performance.
When a decision is taken based on thermal performance only, it can mean that only later does it become clear that a product with a higher compressive strength should have been specified – leading to possible problems with installation or complying with building regulations.
Take a typical ground floor construction. Compared to concrete slab and screed layers, which are capable of bearing greater loads, thermal insulation can be considered the ‘weakest’ layer. It is – or should be – subject to the most scrutiny, although this scrutiny often only happens later in a project.
One possible reason for insulation materials being poorly specified from a compression behaviour point of view could be confusion over how their performance is declared.
Compressive strength and compressive stress
Based on the applicable test methods, behaviour under compression should be talked about as compressive strength or compressive stress.
- When a load is applied to the material and the material fails (is at yield) before it has been compressed by 10% then that load is the compressive strength of the material.
- If the material can be compressed beyond 10% relative deformation before being at yield (e., its compressive strength is not reached) then the load at which 10% relative deformation occurs is the material’s compressive stress at 10% strain.
Across the insulation sector, behaviour under compression is generally compressive strength, as most common insulation materials fail before they are compressed by 10%. Some product literature may say that a given figure is “at yield”, referring to compressive strength.
However, there can be confusing uses of terminology in product literature and certification, especially around the 10% compression threshold. We would always recommend engaging with a manufacturer directly to confirm the exact behaviour.
Alternative compressive strength declarations
Confusion can also arise due to the way declarations are made for other applications. For example, due to the historic use of expanded polystyrene (EPS) insulation in civil engineering projects, where tighter tolerances are required, declarations are made based on 1% compression, as well as 10% compression.
Extruded polystyrene (XPS) is not used in the same applications. With XPS, we don’t make declarations for 1% compression and it is inappropriate to try and equate the two different declarations, as the products are intended for different uses. For typical floor and flat roof insulation applications, a 1% declaration is not relevant.
Why might a structural engineer deviate from compressive strength declarations? While insulation manufacturers make declarations about compression behaviour, typically it is a structural engineer who must determine whether a material’s compressive strength is suitable for the intended application. Insulation manufacturers simply do not have structural engineering qualifications or experience.
It must also be kept in mind that the compressive strength results declared by testing do not equate to the loads that can actually be applied on site. If they did, products would fail in use.
To help keep the use of products within safe limits, factors of safety are employed. Applying a safety factor accommodates uncertainty in the design process, emergency situations, and higher-than-expected loads. However, using a safety factor should not be taken to mean that a construction is ‘safe’ – there are too many other factors in play to draw that conclusion.
Safety factors can be applied at various stages of design and specification. In fact, there is a risk that several can be mixed together, leading to a product being deemed unsuitable even when its use would be acceptable.
For example, following the lead of our BBA third-party certification, Polyfoam XPS uses a safety factor of 2.5 to determine recommended maximum loadings for our products. A structural engineer has actually expressed surprise at how high this safety factor is – after all, the insulation is manufactured in a controlled environment to tight tolerances.
A structural engineer is likely to employ lower safety factors, often from 1.3 to 1.7, depending on their confidence in test data, risk involved, and the likelihood of issues during installation, among other considerations. However, they might also use safety factors in other areas of their calculations.
We have seen, for example, situations where an engineer has taken recommended loadings for a given building use in BS EN 1991-1-1 and applied a safety factor to give a design loading. When a relatively conservative safety factor is also applied to the insulation material’s performance, it’s easy to see how over-specification could start to occur.
Conclusion
Loadings and compression behaviour are a complex topic. For any given project, insulation manufacturers should be just one voice in a conversation that should also feature clients, designers, specifiers, installers and structural engineers. Only through this level of discussion is it possible to be clear about what is required and how best to achieve it, taking into account appropriate safety factors at the right stages.
Want to know more?
For more information on Polyfoam XPS, click here