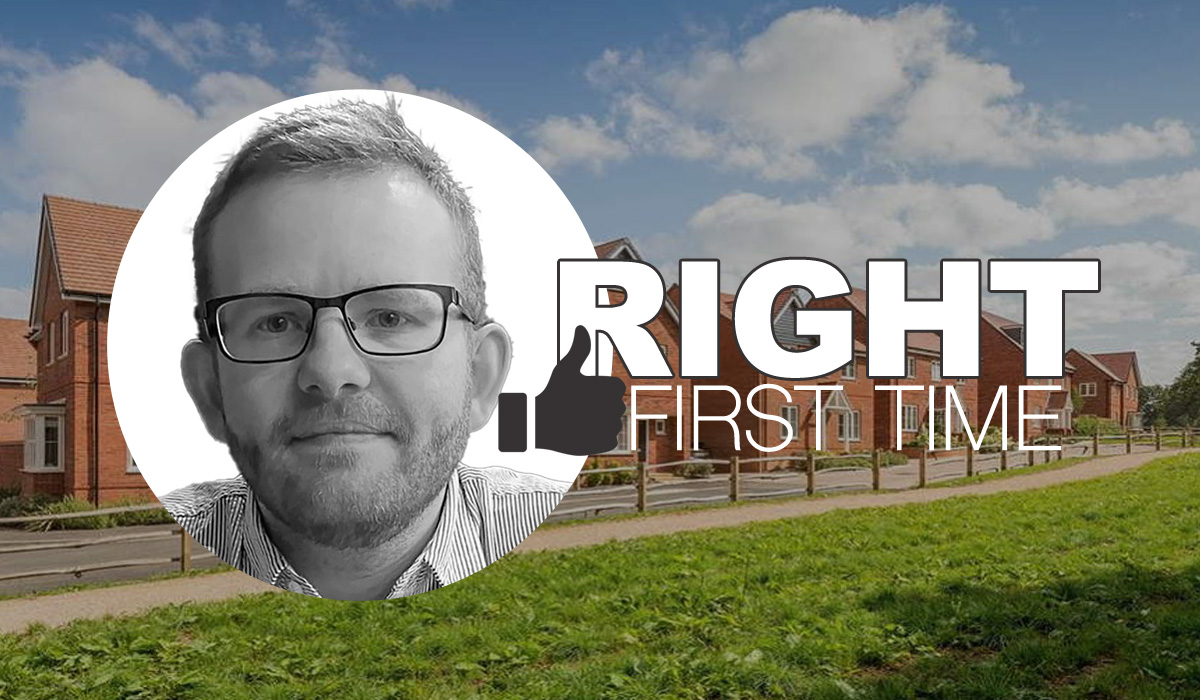
Arron Ross, specification executive at Keystone Lintels provides insight into the Future Homes Standard (FHS) and the fabric first approach to design, and why a one piece thermally-efficient lintel can significantly improve SAP ratings and eliminate the need for costly renewable technologies.
Whilst some net zero policies have been watered down by government in recent months, the FHS will become mandatory in 2025 and remains an excellent opportunity to deliver the energy efficient housing the UK so desperately needs if we are to remain on track with our climate ambitions.
A critical first step is ensuring the fabric of our homes is well designed and by paying careful attention to detailing and thermal bridging, we can get thermal efficiency right first time and eliminate some of the issues that create poorly performing homes.
The updates to Part L requirements of the Building Regulations mark noticeable progress towards the FHS coming in 2025. However realising the goals requires an upfront focus on the design of a building’s envelope without the need for further retrofitting work. The June 2022 interim Part L uplift to energy efficiency requirements demands 31% lower carbon emissions from all new homes through a combination of fabric improvements, low carbon heating technologies and PV panels. But 2025 will bring an even bigger transformation for new housing, with emissions reductions of 75-80% mandated. To achieve such dramatic cuts will require the housebuilding sector to prioritise thermally efficient building fabrics from day one.
Fabric first
To meet these elevated benchmarks for new homes, a fabric-first mentality is essential. Optimising the thermal performance of the building envelope through intelligent design must come first. Constructing an airtight, well-insulated building fabric that minimises heat loss will be key to hitting energy and emissions targets and will go a long way towards achieving compliance, whether for large developments or individual houses.
But the benefits extend beyond reducing carbon emissions. Enhancing the building’s envelope efficiency also provides occupants with superior thermal comfort and air quality.
Building as designed
A critical element of the fabric first approach will be addressing the issue of thermal bridging, which can be responsible for up to 30% of a home’s heat loss. Eliminating thermal bridging through smart design and correct product specification will be essential if we are to ensure we meet these ambitious new regulations.
While there are some design, measurement and calculation issues, the other concern in terms of thermal bridging is that we are not building consistently what we design, or we are not detailing the right products in the right places. There are also issues with site skills and workmanship; when you fail to build correctly it undermines the good work carried out in the first place.
This can lead to a performance gap between as- designed and as-built building performance. It’s why these weak spots can have a significant impact on a building’s heat loss and have a detrimental effect on the overall fabric efficiency of the dwelling.
All materials specified in the Building Regulations Part L report (BREL) must be installed with no substitutions allowed unless the report is recreated or amended by an energy assessor. Building control can use this report as a checklist and may ask for thermal elements to be recalculated if you swap brands or material types of different thermal values.
Part L now also states that we use the actual thermal transmittance values for building products within the envelope of a dwelling; whereas in the past, generic ACD (accredited construction detail) values were accepted within the SAP assessment. These values could vary rather substantially from the actual value of a specific product. By making this change, the Y value obtained is now accurately represented within the BREL report.
Photographic evidence
One of the stand out changes from Part L to help bridge the performance gap is the requirement of photographic evidencing of key junctions at the relevant construction stage for every new dwelling. This will need to have geo-location technology activated, and the report will be provided to building control and the building owner. Essentially, there will need to be proof that the dwelling has been constructed from the same materials that it was designed from; ensuring the property runs as efficiently as it should.
High performance lintel
Traditional steel lintels can create a significant thermal bridge in homes due to the high thermal conductivity of steel and because they span over long lengths in a typical build. However, solutions, such as Hi-therm+, can address this, setting a new standard for thermal efficiency in steel lintels. By incorporating a thermal break, it is up to five times more thermally efficient than a standard lintel.
Such lintels have made a significant impact on the thermal efficiency of homes and are specified on many housebuilder projects around the UK due to its low cost and improved performance in lowering carbon emissions within the Standard Assessment Procedure (SAP).
When you consider the BRE has found that thermal bridging can account for up to 30% of heat loss from buildings, then paying close attention to the details and structural elements such as lintels can have a huge impact on the overall thermal performance of a building.
Want to know more?
For further information, please contact David Ing at Fabrick