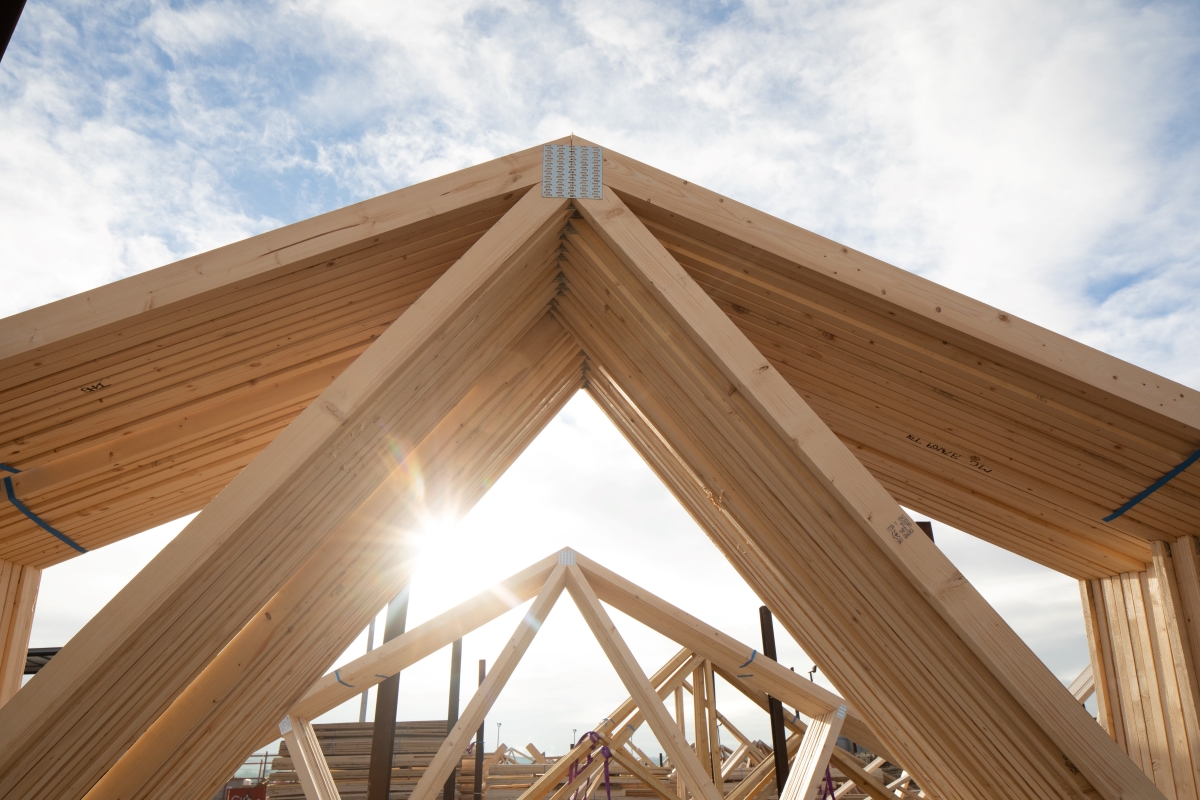
Navigating quotes can be challenging, and when the market is tough, every penny is under scrutiny. Occasionally, the numbers might come back vastly different, but the reality of the quote might not be all it seems – with hidden costs, cut corners and misinterpretations leading to complications later in the project.
To try to make things a bit clearer, Oli James Technical Director of leading truss manufacturer, Donaldson Timber Engineering, has answered a few common questions about how to seek out the most suitable quotes for your project.
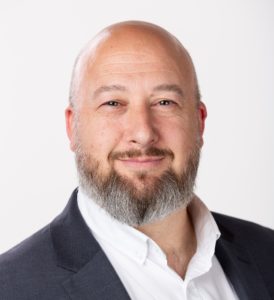
What are the common pitfalls when assessing truss quotes?
It’s crucial that you read your quotes carefully and question anything you don’t understand. It’s also important to get an idea of timescales early on as this can have a major impact on the overall project. For example, a quotation may take two weeks and delivery periods can vary from two to six weeks depending on the manufacturer and the time of year.
The quote you receive is likely to vary from company to company as some suppliers will simply provide an overall cost, whereas others will contribute a more detailed document to show exactly what you are paying for. Make sure you know what each quote covers before making your decision.
Many people assume each quote will include everything they need to pay for, but this is not always the case. Some companies do not include items like gable straps & noggins, wall plate and wall plate straps in the price so check this has been included as it can make a huge difference. Gable straps noggins, wall plate and wallplate straps alone can affect the price of a house by up to 15% of the quote!
What information do truss manufacturers need to produce an accurate quote?
Customers need to be clear on what they want to be included in the price, as there is a big variance in what we’re asked to supply. Sometimes we receive a request for ‘everything above wall plate’, but this doesn’t capture the specifics. To be clear, items to be included in the quote should be listed to avoid ambiguity.
Ideally, manufacturers need floor plans, sections, elevations, eaves details and any relevant Standard Details relating to the roof – such as a chimney, solar panels, dormers, rooflights or anything that can affect the design of the roof.
If a manufacturer has these details, it’s a very good starting point to preparing an accurate quote.
What should a good quote include?
A good quote should be fully itemised and quantified, with a short description for each line so there’s no uncertainty. If you’re unsure of any of the terminology, it should be clarified with the designer. It sounds obvious, but it should also include everything that you have asked for and ideally, every item needed to complete the project.
If everything is added into the package, it’s one less thing to source elsewhere and ensures that everything required has been factored in. It’s better to receive a long quote where every part has been considered, than start with a cheaper quote and realise crucial parts have been left off. It’s easy to remove items that are not required than having to consider what hasn’t been accounted for.
Its also good to check that sufficient wastage has been included on bracing and infill quantities.
How do you know the price is right?
Start by checking quantities, sizes and the specification list. No two quotes will ever be the same, but these basics should all be included.
Once you have the standard items, make sure all ancillaries are included. If something has been included in your drawings, it must be part of the quote to be compliant.
It’s also worth remembering that value is not just cost effectiveness; you are paying for confidence in who you will work with. Find a company who you trust to deliver on time and quality. Check their credentials and history before committing.
What happens next?
When you’ve agreed a fixed quote and are happy to proceed you should receive layout drawings for approval. These should contain all relevant dimensions for checking; truss profiles; relevant loading information and notes relating to areas of complexity or assumptions made from the drawings provided. You should ensure that these details are all checked thoroughly by a competent person and any changes clearly marked on the drawing before returning to the designer. These changes should then be made by the designer and a final approval drawing issued to you for sign-off and to then confirm your delivery date.
Manufacturing will usually commence a few days prior to delivery. It is important that a suitable delivery date is agreed and that you arrange for the necessary equipment for offloading. The Trussed Rafter Association recommends offloading by mechanical means, but also stipulates that any truss over 75kg must be mechanically offloaded.
When your delivery arrives, the driver will have a copy of the layout drawing with his delivery paperwork and should have suitable method statements for offloading in accordance with how the vehicle has been loaded.
For more support, get in touch with our sales team via our website: www.donaldsontimberengineering.co.uk