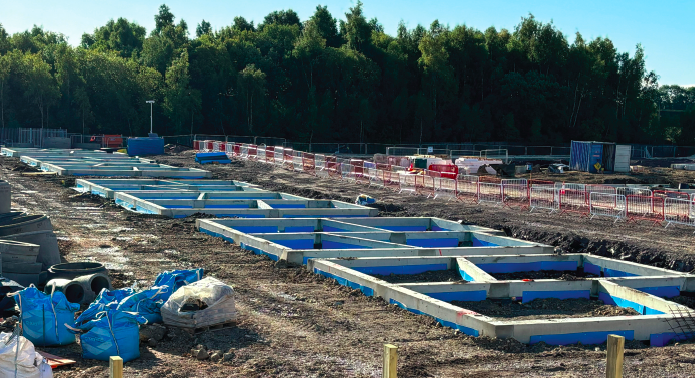
Green Piling explains how its latest solution for housebuilders, G-sPan, a piled precast foundation system, is a great alternative to traditional in-situ ground beams, which can be installed all year round.
Excavating trenches in the UK, where it rains on half of the days of the year, and is only increasing thanks to the effects of climate change, increases the risk profile of any build. Deep trenches can require shoring, edge protection, groundwater management and, on applicable sites with cohesive soils, additional costs for heave protection materials.
With that in mind, Green Piling has launched its G-sPan foundation beams, a new solution designed to enhance support and stability for residential structures. By introducing the new G-sPan foundation beams, the foundation engineering company aims to address key challenges in the construction industry, including efficiency, sustainability and long-term structural performance.
Eliminating hidden costs
Colin Thompson, Business Development Manager of Green Piling explains: “With an industry leading beam breadth of only 350mm, the narrow width of the system not only reduces the use of concrete in each foundation but ensures the foundation itself does not clash with any service entry points or SVP [soil vent pipe] egress, which allows the foundation to be constructed at an optimum height. “With the foundation sitting higher in the ground, this reduces the requirement for costly excavation of working platforms and subsequent reinstatement, an often hidden cost associated with other precast foundations.”
Wordsworth Property Developments managing director, Jonathan Bailey was one of the first companies to employ the G-sPan foundation system. He said the build solution offered by Green Piling suited their project’s requirements well. “The driven pile and pre-cast ring beam system allowed the imported material, used to cap off the made ground below, to remain in place,” he added. “This method simplified and de-risked the earthworks strategy and. material management plan considerably.
It also resulted in a cost saving, and a significant time reduction compared to strip footings.”
Off-site benefits
Off-site construction methods are becoming increasingly popular in the housebuilding market, and with good reason too. The G-sPan beams are manufactured off-site in Chesterfield in a controlled environment, ensuring consistent quality and precise specifications. This centralised production helps to facilitate reliable delivery schedules and efficient construction timelines.
The benefits to an off-site production approach don’t stop there either, it also reduces on-site labour and material waste, enabling housing developers to complete projects quicker and achieve cost savings.
As a specialist geotechnical contractor, Green Piling specialises in the design, supply and installation of continuous flight auger (CFA), precast concrete and steel tube piles, as well as contiguous and secant retaining walls and projects with restricted access or headroom.
Mythbusting
“But piling is expensive, isn’t it?” is the general perception in the housebuilding industry and, compared to concrete strip foundations, having specialist plant attend site to install the support for buildings will, of course, be a bit more costly but what about building where the ground won’t allow traditional foundations? Housebuilders can often view any expenditure below DPC level as a necessary evil, but the reality is that a trusted geotechnical partner can save money over the course of a build.
Trenchfill systems, where foundations are required to be deeper than usual, can be costly as:
- The excavated material can be costly to export, especially if brownfield development
- Poor ground can require expensive shoring systems to be required during construction
- The carbon expense of the foundation increases due to the CO2 of the concrete plus the numerous vehicle movements required to deliver it to site
Site investigation
Early consultation when appraising land is one such service offered by Green Piling to help minimise the risks associated with deep trenches. By determining the likely geotechnical solutions required on a site and forming an estimate of the associated costs, land buyers can negotiate any deal to purchase with minimal exposure. Key to that appraisal is a thorough Site Investigation to document the condition of the ground and the likely impact of the build on it, both during construction and over the lifespan of the buildings.