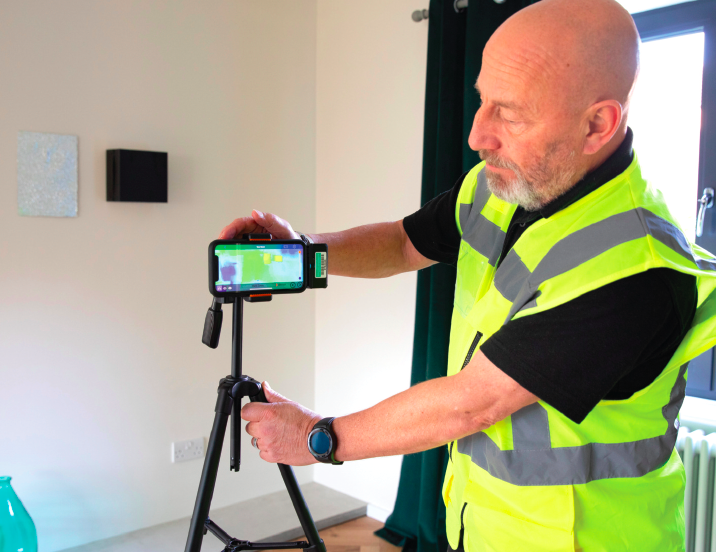
PHPD talks to Dr. Richard Jack, technical director of Build Test Solutions, to learn all about Measured Energy Performance and why this will be a key consideration in housebuilding and retrofitting once the Future Homes Standard 2025 takes effect.
The advent of this year brings with it the coming of the much-anticipated Future Homes Standard 2025 (FHS). This new set of rules is set to revolutionise how homes are built in the UK, with a 75-80% reduction in carbon emissions compared to the current regulations. How these lower emissions are going to be achieved is still up in the air. While a mixture of fabric and low carbon heat sources would be optimal, low uptake on heat pumps and a boiler ban reversal mean the burden of low emissions will likely fall on the former. The air tightness of new homes and how much heat they can store is likely to be top priority. While this may be a challenge for smaller builders wanting to know how they can abide by these new regulations. There are tools out there at your disposal. Someone well versed in this very topic is Dr. Richard Jack, Technical Director of Build Test Solutions, who caught up with us on the Professional Builder Podcast to explain why measured energy performance is set to be the new way forward.
First Richard, who has a PHD in the measured energy performance (MEP) of buildings, explains what MEP is: “What we’re particularly talking about is measuring physical aspects of the energy performance of the building. “The sorts of things we would measure would be air tightness, (the most familiar to people) U values of individual elements (heat loss performance of a wall, a floor, a ceiling) and the overall thermal performance of the building. This is the heat transfer coefficient, and basically represents the total amount of heat loss from every source, including air tightness, ventilation and the fabric performance.”
How this works in practice can be in a number of ways, which Richard outlines. As these measurements can be done for new builds or existing buildings (opening up a whole avenue for retrofit), there are some methods which take longer and involve measuring smart meter readings and the internal temperature of a building over the space of a few weeks. The main way for heat transfer coefficients that would be applicable for new builds would be an overnight test though. For U-values, Richard explains what Build Test Solutions does: “If you’re going to measure U values, this involves a much shorter test where you bring in some bespoke hardware plus a thermal camera and a temperature controller.
“So what we’re going to do in this case is keep the internal temperature of one room super steady with this temperature controller. Then we’re going to measure the amount of heat transfer in those steady state conditions and then divide it by the temperature difference between inside and outside. That gives you the U value.” Particular wall, floor – or practically any other elements – can be measured and compared with their design in just an hour. Air tightness, which many will already be familiar with, can be measured in just half an hour or so.
The outcome of this kind of measuring is a grade given to the overall building, breaking down exactly how it performs in each of the categories. It’s all well and good selecting the best materials available, but anything can happen on site. Whether it’s insulation that’s not quite overlapped right, or it’s not close enough to the wall and there’s air movement behind it creating thermal bypass, even the most minor of mistakes can have a big impact on the final performance of a home. Without actually measuring the heat loss or the air tightness, we have no sure way of knowing how well a building actually performs. Why does this matter though? Well, as well as saving some money on bills for the future homeowner of the house you’re building, you also want to make sure you’re complying with the latest regulations on air tightness, which is expected to be a key part of the Future Homes Standard 2025.
More than this, builders are able to accurately specify the correct heat source (heat pump size, for example) and emitter depending on how well a building performs. There’s another element in the proposed FHS 2025 though, that is also key for builders trying to stand out from the crowd with their new-builds. Richard explains: “There’s a new voluntary standard being suggested in the consultation, whereby you would get a government endorsed quality mark that says this building is of really high performance. But only if you measured the heat transfer coefficient of the building and proved it worked as planned.
So, it’s not a mandatory part of what’s being suggested in the consultation but it’s a voluntary way of builders saying ‘we really believe it’s important to make sure that the actual building performs as expected in real life and we’ve tested it and it does’. It’s sort of the idea of proving that it does what it says on the tin. “All of your systems are going to be replaced on a 10, 20, 30 year cycle. But your fabric is going to be there forever.”