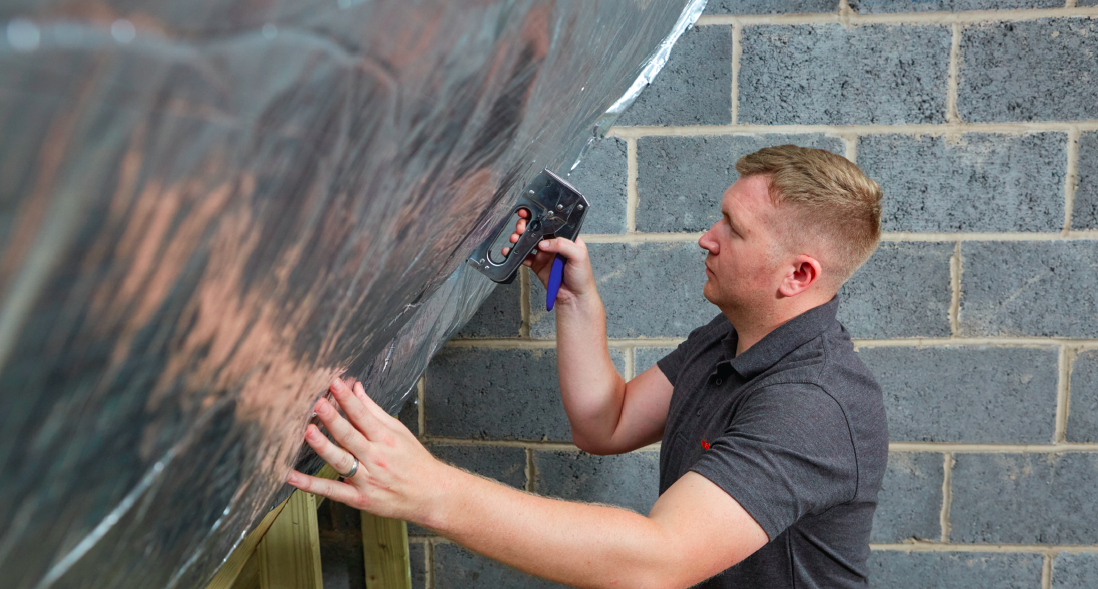
In an effort to decarbonise the built environment, homes and other buildings must now be built to a higher, more energy efficient standard. Here, Mike Vaczi, technical Director at YBs by soPrEMA looks at the current and future requirements and explain how the tightening standards can be met.
With the serious impact of global greenhouse gas emissions now increasingly obvious, the drive to achieve net zero by 2050 has become a priority. In the UK, the built environment accounts for approximately 30% of the country’s greenhouse gas emissions, of which heating is the main source, accounting for 23% of the total itself. Therefore, to achieve the net zero target there needs to be a significant change to the energy efficiency of buildings.
One of the key steps in this process was the update to Part L of the Building Regulations, which fully came into force in June 2023 following a 12-month transition period. The new standards for energy efficiency aimed to achieve a 30% reduction in emissions from new homes and a 27% reduction for other buildings.
Another crucial step in the move toward more energy efficient buildings is the Future Homes and Buildings Standard, which is set to be introduced in 2025. This will raise the energy efficiency standards for new builds and major renovation projects still further. A Government consultation on the exact requirements of the Future Homes and Buildings Standard concluded earlier this year, with the response still to be published. In the current proposals there are two notional building specifications for new homes, however both options would include the same U-value targets:
Roof: 0.11 w/m2K
External wall: 0.18 w/m2K
Floor: 0.13 w/m2K
Window: 1.2 w/m2K
Door: 1.0 w/m2K
This marks a significant tightening of standards compared with the Part L 2016 requirements, which homes were built to until the most recent uplift. In fact, it is a 45% change in the roof U-values, 40% for that of external walls and 48% for floor Uvalues. Although necessary on the path to decarbonisation, the targets will be a challenge to meet and will require an increased focus on minimising heat loss when designing each element of the home.
The key question is how can the required performance be achieved? Well, it’s clear that achieving the target U-values laid out in the Future Homes and Buildings Standard will require a strongly fabric first approach, where thermal improvements to the structure of the building are prioritised over the use of additional technologies to achieve energy efficiency. This means that insulation and airtightness must be maximised.
There are several factors to consider when designing and installing insulation to ensure its effectiveness is maximised. The first and perhaps most obvious is that a holistic approach needs to be taken, whereby the insulation of the roof, walls and floors are all considered, alongside minimising heat loss from windows, doors and other thermal bridges in the structure. In addition, the available space is a consideration. The thickness of the insulation is often, although not always, linked to the performance it delivers, particularly for PIR insulation. Therefore, it is essential to ensure there is sufficient space in the rafters, wall cavities or under floors to fit the required thickness of insulation. For example, most new homes will be designed with rafter thicknesses of 200mm or more to accommodate the insulation.
It is also important to remember that different types of insulation work in distinctive ways, so combining these products together can help minimise the different forms of heat loss. For example, using PIR insulation between the rafters, which prevents conduction, and overlaying this with a multifoil product, which reflects infrared back, will prevent all forms of heat transfer – conduction, convection, and radiation. Furthermore, as homes become more airtight and well insulated, the risk of overheating increases, which is why Part O: Overheating was created within the Building Regulations alongside the most recent updates to Part L. Therefore, minimising heat transfer through radiation. also has a further advantage. Not only will. this type of insulation help reflect heat back in during the winter but will provide an effective barrier against solar overheating in the summer, minimising the need for mechanical cooling.
Finally, it is always important to look for products that have third party accreditation to help ensure they will deliver the performance levels stated by the manufacturer. KIWA BDA and the British Board of Agrément (BBA) are among the most widely recognised third party testing accreditations in the industry and will confirm the performance. Other certifications, such as the National House-Building Council’s NHBC Accepts are also important to look for, especially if the new home is covered by NHBC warranty and insurance policies.